گرافت كۆپ ئۇچرايدىغان مېتال بولمىغان ماتېرىيال بولۇپ ، قارا ، يۇقىرى ۋە تۆۋەن تېمپېراتۇرىغا چىداملىق ، ئېلېكتر ۋە ئىسسىقلىق ئۆتكۈزۈشچانلىقى ياخشى ، سىلىقلاش مېيى ۋە مۇقىم خىمىيىلىك ئالاھىدىلىككە ئىگە. ياخشى توك ئۆتكۈزۈشچانلىقى ، EDM دا ئېلېكترود ئورنىدا ئىشلىتىشكە بولىدۇ. ئەنئەنىۋى مىس ئېلېكترودقا سېلىشتۇرغاندا ، گرافتنىڭ يۇقىرى تېمپېراتۇرىغا چىداملىق ، تۆۋەن توك چىقىرىش ۋە كىچىك ئىسسىقلىق ئۆزگىرىشى قاتارلىق نۇرغۇن ئەۋزەللىكى بار. ئۇ ئىنچىكە ۋە مۇرەككەپ زاپچاسلار ۋە چوڭ تىپتىكى ئېلېكترودلارنى بىر تەرەپ قىلىشتا تېخىمۇ ياخشى ماسلىشىشچانلىقىنى كۆرسىتىپ بېرىدۇ. ئۇ ئاستا-ئاستا مىس ئېلېكترودنىڭ ئورنىنى ئېلېكتر ئۇچقۇسىغا ئالماشتۇردى. ئېلېكترودنى پىششىقلاشنىڭ ئاساسىي ئېقىمى [1]. ئۇنىڭدىن باشقا ، گرافت ئۇپراشقا چىداملىق ماتېرىياللارنى ماي سۈرتمەي تۇرۇپ يۇقىرى سۈرئەتلىك ، يۇقىرى تېمپېراتۇرا ۋە يۇقىرى بېسىملىق شارائىتتا ئىشلىتىشكە بولىدۇ. نۇرغۇن ئۈسكۈنىلەردە گرافت ماتېرىيالى پورشېن لوڭقىسى ، پېچەتلەش ۋە تىرەك قاتارلىقلار كەڭ قوللىنىلىدۇ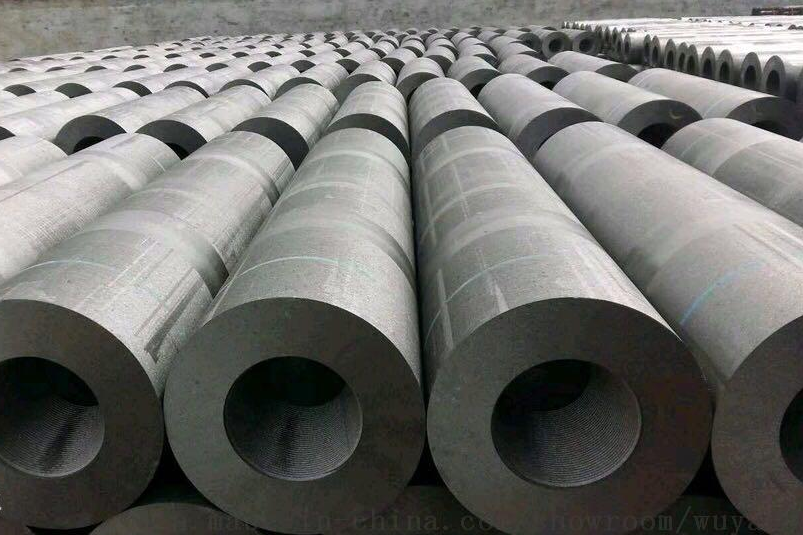
ھازىر گرافت ماتېرىياللىرى ماشىنا ، مېتاللورگىيە ، خىمىيىلىك سانائىتى ، دۆلەت مۇداپىئەسى ۋە باشقا ساھەلەردە كەڭ قوللىنىلىۋاتىدۇ. گرافت زاپچاسلىرى ، مۇرەككەپ زاپچاسلارنىڭ قۇرۇلمىسى ، يۇقىرى ئېنىقلىق دەرىجىسى ۋە يەر يۈزىنىڭ سۈپەت تەلىپىنىڭ نۇرغۇن تۈرلىرى بار. گرافت پىششىقلاپ ئىشلەشتىكى دۆلەت ئىچى تەتقىقاتى يېتەرلىك ئەمەس. دۆلەت ئىچىدىكى گرافت پىششىقلاپ ئىشلەش ماشىنىسى قوراللىرىمۇ بىر قەدەر ئاز. چەتئەل گرافت پىششىقلاپ ئىشلەش ئاساسلىقى گرافت پىششىقلاپ ئىشلەش مەركىزىنىڭ يۇقىرى سۈرئەتلىك بىر تەرەپ قىلىش مەركىزىنى ئىشلىتىدۇ ، ئۇ ھازىر گرافت پىششىقلاپ ئىشلەشنىڭ ئاساسلىق تەرەققىيات يۆنىلىشىگە ئايلاندى.
بۇ ماقالە ئاساسلىقى گرافىك پىششىقلاپ ئىشلەش تېخنىكىسى ۋە پىششىقلاپ ئىشلەش ماشىنىسى قوراللىرىنى تۆۋەندىكى تەرەپلەردىن تەھلىل قىلىدۇ.
Graf گرافت پىششىقلاپ ئىشلەش ئىقتىدارىنى ئانالىز قىلىش
Graph كۆپ ئىشلىتىلىدىغان گرافت پىششىقلاپ ئىشلەش تېخنىكىسى تەدبىرلىرى
Graf گرافىكنى بىر تەرەپ قىلىشتا كۆپ ئىشلىتىلىدىغان قوراللار ۋە كېسىش پارامېتىرلىرى
گرافىك كېسىش ئىقتىدار ئانالىزى
گرافت بولسا بىر خىل ئوخشىمىغان قۇرۇلما بولۇپ ، پارچىلىنىدىغان ماتېرىيال. گرافت كېسىش گرافت ماتېرىيالىنىڭ سۇنۇق يېرىلىشى ئارقىلىق ئۈزۈلۈپ قالغان ئۆزەك زەررىچىسى ياكى پاراشوك ھاسىل قىلىش ئارقىلىق ئەمەلگە ئاشىدۇ. گرافت ماتېرىياللىرىنى كېسىش مېخانىزمىغا قارىتا ، دۆلەت ئىچى ۋە سىرتىدىكى ئالىملار نۇرغۇن تەتقىقاتلارنى ئېلىپ باردى. چەتئەللىك ئالىملارنىڭ قارىشىچە ، قورالنىڭ كېسىش گىرۋىكى ئەسەر بىلەن ئۇچراشقاندا ، گرافت ئۆزەك ھاسىل قىلىش جەريانى ئاساسەن بولىدۇ ، ھەمدە قورالنىڭ ئۇچى ئېزىپ ، كىچىك ئۆزەك ۋە كىچىك ئورەك ھاسىل بولىدۇ ، ھەمدە يېرىلىش ھاسىل بولىدۇ ، بۇ قورال قورالنىڭ ئالدى ۋە ئاستى تەرىپىگە سوزۇلۇپ ، سۇنۇق ئورەك ھاسىل قىلىدۇ ، ھەمدە ئەسەرنىڭ بىر قىسمى بۇزۇلۇپ ، ئۆزەك ھاسىل بولىدۇ. دۆلەت ئىچىدىكى ئالىملارنىڭ قارىشىچە ، گرافت زەررىچىلىرى ئىنتايىن ئىنچىكە بولۇپ ، قورالنىڭ كېسىش گىرۋىكىدە چوڭ ئۇچى بار ، شۇڭا كېسىش گىرۋىكىنىڭ رولى چىقىرىشقا ئوخشايدۇ. قورالنىڭ ئالاقىلىشىش رايونىدىكى گرافت ماتېرىيالى - خىزمەت ئەسىرى تىرناق يۈزى ۋە قورالنىڭ ئۇچى تەرىپىدىن قىسىلىدۇ. بېسىم ئاستىدا ، سۇنۇق سۇنۇق ھاسىل بولىدۇ ، بۇ ئارقىلىق ئۆزەك ئۆزىكى ھاسىل بولىدۇ [3].
گرافت كېسىش جەريانىدا ، ئەسەرنىڭ يۇمىلاق بۇلۇڭى ياكى بۇلۇڭىنىڭ كېسىش يۆنىلىشىنىڭ ئۆزگىرىشى ، ماشىنا قورالىنىڭ تېزلىنىشىدە ئۆزگىرىش ، قورالنى كېسىش ۋە سىرتقا چىقىش يۆنىلىشى ۋە بۇلۇڭىنىڭ ئۆزگىرىشى ، تەۋرىنىش كېسىش قاتارلىقلار سەۋەبىدىن ، گرافت ئەسەرنىڭ مەلۇم گىرۋىكى كېلىپ چىقىدۇ. بۇلۇڭ-پۇچقاق ۋە ئۆزەك ، ئېغىر قوراللارنىڭ ئۇپرىشى ۋە باشقا مەسىلىلەر. بولۇپمۇ بۇلۇڭ ۋە نېپىز ۋە تار قوۋۇرغا گرافت زاپچاسلىرىنى بىر تەرەپ قىلغاندا ، ئەسەرنىڭ بۇلۇڭى ۋە ئۆزەكلىرىنى كەلتۈرۈپ چىقىرىشى مۇمكىن ، بۇمۇ گرافت پىششىقلاپ ئىشلەشتىكى قىيىنچىلىققا ئايلاندى.
گرافىك كېسىش جەريانى
گرافت ماتېرىياللىرىنىڭ ئەنئەنىۋى پىششىقلاپ ئىشلەش ئۇسۇللىرى بۇرۇلۇش ، تۈگۈش ، ئۇۋىلاش ، تىكىش قاتارلىقلارنى ئۆز ئىچىگە ئالىدۇ ، ئەمما ئۇلار ئاددىي شەكىل ۋە ئېنىقلىق دەرىجىسى تۆۋەن بولغان گرافت زاپچاسلىرىنى بىر تەرەپ قىلىشنى ئەمەلگە ئاشۇرالايدۇ. گرافت يۇقىرى سۈرئەتلىك پىششىقلاپ ئىشلەش مەركىزى ، كېسىش قوراللىرى ۋە مۇناسىۋەتلىك قوللاش تېخنىكىلىرىنىڭ تېز تەرەققىي قىلىشى ۋە قوللىنىلىشى بىلەن ، بۇ ئەنئەنىۋى پىششىقلاپ ئىشلەش ئۇسۇللىرى ئاستا-ئاستا تېز سۈرئەتتە پىششىقلاپ ئىشلەش تېخنىكىسىنىڭ ئورنىنى ئالدى. ئەمەلىيەت شۇنى ئىسپاتلىدىكى: گرافتنىڭ قاتتىق ۋە سۇنۇق ئالاھىدىلىكى سەۋەبىدىن ، پىششىقلاپ ئىشلەش جەريانىدا قوراللارنىڭ ئۇپرىشى تېخىمۇ ئېغىر بولىدۇ ، شۇڭا ، كاربون ياكى ئالماس سىرلانغان قوراللارنى ئىشلىتىش تەۋسىيە قىلىنىدۇ.
كېسىش جەريانى تەدبىرلىرى
گرافتنىڭ ئالاھىدىلىكى سەۋەبىدىن ، گرافت زاپچاسلىرىنى ئەلا سۈپەتلىك بىر تەرەپ قىلىشنى ئىشقا ئاشۇرۇش ئۈچۈن ، مۇناسىپ جەريان تەدبىرلىرىنى قوللىنىشى كېرەك. گرافت ماتېرىيالىنى يىرىكلەشتۈرگەندە ، بۇ قورال بىر قەدەر چوڭ كېسىش پارامېتىرلىرىنى ئىشلىتىپ ، خىزمەت ئەسىرىنى بىۋاسىتە باقالايدۇ. پىششىقلاپ ئىشلەش جەريانىدا ئۆزەكتىن ساقلىنىش ئۈچۈن ، ياخشى ئۇپراشقا چىداملىق قوراللار دائىم قورالنىڭ كېسىش مىقدارىنى ئازايتىشقا ئىشلىتىلىدۇ ، ھەمدە كېسىش قورالىنىڭ مەيدانىنىڭ قورالنىڭ دىئامېتىرىنىڭ 1/2 دىن تۆۋەن بولۇشىغا كاپالەتلىك قىلىڭ ھەمدە ئىككى ئۇچىنى بىر تەرەپ قىلغاندا ئاستىلىتىش بىر تەرەپ قىلىش قاتارلىق جەريان تەدبىرلىرىنى ئىجرا قىلىڭ [4].
كېسىش جەريانىدا كېسىش يولىنى مۇۋاپىق ئورۇنلاشتۇرۇش كېرەك. ئىچكى قىياپەتنى بىر تەرەپ قىلغاندا ، ئەتراپتىكى كونتېينېرنى ئىمكانقەدەر ئىشلىتىپ ، كېسىلگەن قىسمىنىڭ كۈچ قىسمىنى كېسىپ ، قېلىن ھەم كۈچلۈك بولۇشى ھەمدە ئەسەرنىڭ بۇزۇلۇشىنىڭ ئالدىنى ئېلىش كېرەك [5]. ئايروپىلان ياكى ئوقلارنى بىر تەرەپ قىلغاندا ، ئىمكانقەدەر دىئاگونال ياكى ئايلانما يەم-خەشەكنى تاللاڭ. قىسىمنىڭ خىزمەت يۈزىدىكى ئاراللاردىن ساقلىنىڭ ، خىزمەت يۈزىدىكى ئەسەرنى كېسىشتىن ساقلىنىڭ.
ئۇنىڭدىن باشقا ، كېسىش ئۇسۇلىمۇ گرافت كېسىشكە تەسىر كۆرسىتىدىغان مۇھىم ئامىل. تۆۋەن ئورۇش جەريانىدا كېسىش تەۋرىنىشى يۇقىرى ئورۇشتىن تۆۋەن. تۆۋەن ئورۇش جەريانىدا قورالنىڭ كېسىش قېلىنلىقى ئەڭ يۇقىرى چەكتىن نۆلگە تۆۋەنلەيدۇ ، قورال خىزمەت بۇيۇمىغا كېسىلگەندىن كېيىن قاڭقىش ھادىسىسى بولمايدۇ. شۇڭلاشقا ، گرافت پىششىقلاپ ئىشلەش ئۈچۈن ئادەتتە تۆۋەن زاۋۇت تاللىنىدۇ.
گرافىك ئەسەرلىرىنى مۇرەككەپ قۇرۇلمىلار بىلەن بىر تەرەپ قىلغاندا ، يۇقىرىدىكى ئويلىنىشلارغا ئاساسەن پىششىقلاپ ئىشلەش تېخنىكىسىنى ئەلالاشتۇرۇشتىن باشقا ، ئەڭ ياخشى كېسىش نەتىجىسىنى قولغا كەلتۈرۈش ئۈچۈن چوقۇم كونكرېت شارائىتقا ئاساسەن بەزى ئالاھىدە تەدبىرلەرنى قوللىنىش كېرەك.
يوللانغان ۋاقتى: 2-ئاينىڭ 20-كۈنىدىن 20-كۈنىگىچە